Idén májusban részt vettem egy befektetőknek szóló üzleti ebéden, ahol többek közt Osamu Suzuki, a japán Suzuki Motor Corporation elnöke is beszédet mondott. Az immár 89 éves, legendás cégvezető, aki 1978 óta áll a világ 11. legnagyobb autógyárának élén, felidézte a magyarországi Suzuki gyár megalapításának történetét: Többéves egyeztetési folyamatot követően 1990. januárjában írta alá a megállapodást Medgyessy Péter miniszterelnök-helyettessel és Lepsényi Istvánnal, az Autókonszern Rt. ügyvezetőjével arról, hogy Esztergomban vegyesvállalatot hoznak létre. Mivel Magyarországon akkor zajlott az államszocialista rendszer felszámolása és a demokratikus állammá való átalakulás (az első szabad választásokra 1990 tavaszán került sor), befektetői szemmel nézve Osamu Suzuki döntése nem volt éppen kockázatmentes. Mindenesetre bizalmat szavazott Magyarországnak. Én pedig Suzuki úr beszédének hatására kedvet kaptam ahhoz, hogy felkeressem az esztergomi Suzuki-gyárat és beregisztráltam egy gyárlátogatásra.
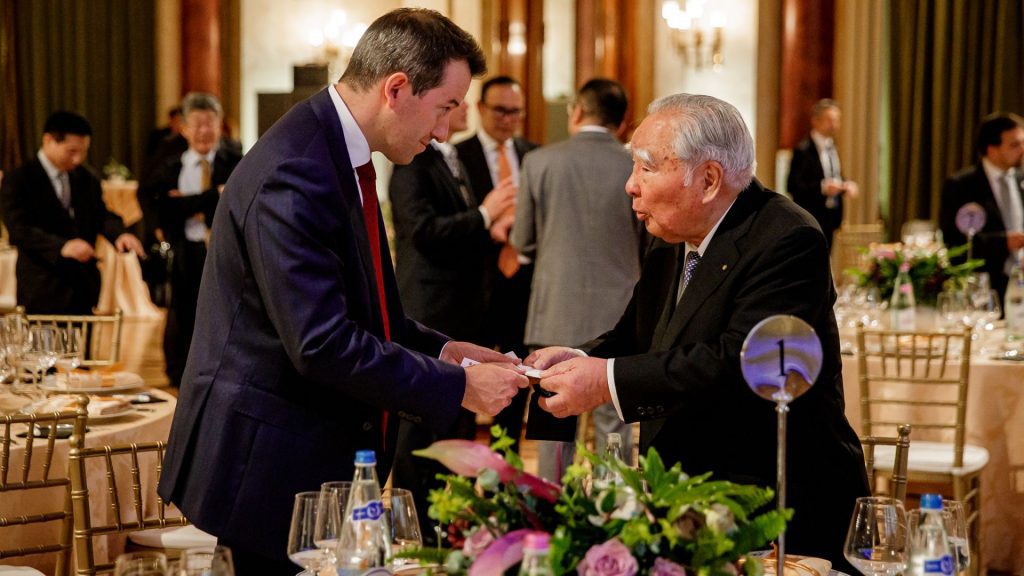
A megadott időpontnál 20-25 perccel hamarabb már a gyár személyi bejárójánál gyülekezett a gyárlátogatásra váró csoport. Mindenki leadta az előre kitöltött regisztrációs lapját a portán, majd hamarosan mehettünk is befelé. A kapu túloldalán azonnal kaptunk egy védősisakot és egy szemüveget. (Előbbit a gyár egész területén viselni kellett, utóbbit csak a hegesztőüzemben tett látogatás során.) Utána egy előadóterem irányába tereltek minket. Ahogy a gyár épületei között áthaladtunk, egyből feltűnt, hogy a dolgozók hosszú, sötétkék nadrágot és a munkavédelmi bakancsot viseltek.
A Suzuki előre jelezte, hogy biztonsági okokból a hegesztőüzembe nem engednek be senkit szandálban, rövidnadrágban és rövid ujjú pólóban. Ezért meglepett, hogy a nem megfelelően felöltözött látogatók szinte palotaforradalmat robbantottak ki a 35 fokos melegre hivatkozva. A gyárlátogatás szervezői (többnyire nyugdíjas Suzuki dolgozók) ragaszkodtak az előíráshoz és csak azokon tudtak csak segíteni, akik hajlandóak voltak rövid ujjú pólóikra egy hosszú ujjú Suzukis kabátkát felvenni. Egyébként pedig felhívták a figyelmet arra, hogy a Suzuki dolgozóinak az időjárástól függetlenül mindig tartaniuk kell magukat az öltözködési előírásokhoz.
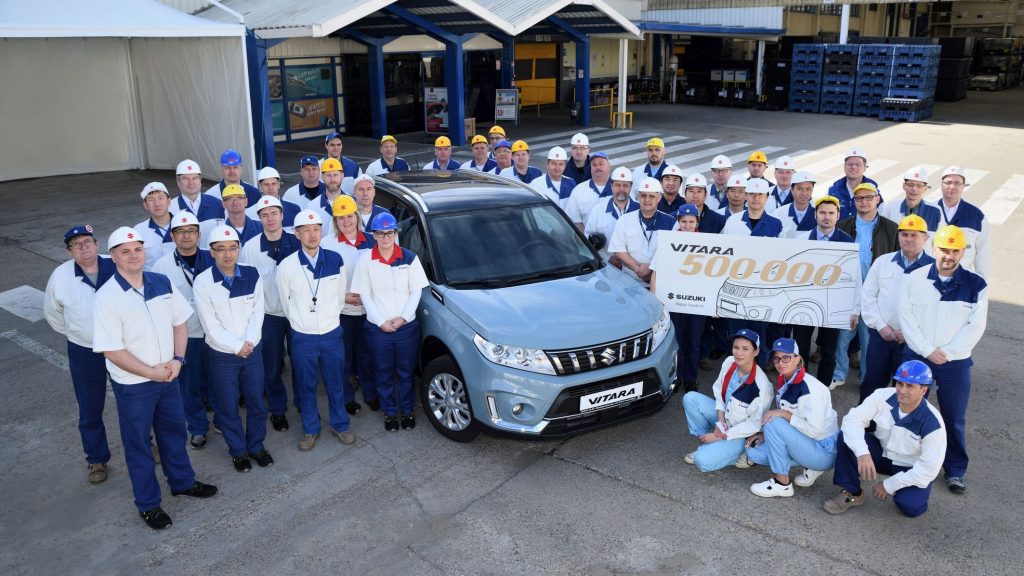
Amíg lezajlott a fenti vita, alkalmam volt kicsit szemlélődni az előadóteremben. A falon hatalmas tábla hirdeti a Suzuki 2019-es alapelveit magyar és japán nyelven is:
- 2030-ig megerősítik a kapcsolataikat minden partnerükkel.
- Mindig a minőséget tartják szem előtt.
- A végellenőrzésen 100% megfelelőségi arány elérése a cél.
- A biztonsági és minőségi alapelvekhez hűen alakítják ki a genbát (azaz az értékteremtés helyét, jelen esetben a gyártóterületet) és a gyártástechnológiát.
- A biztonság az első.
Közben körülbelül 35-en gyűltünk össze. A gyárlátogatók az ország minden tájáról érkeztek. Voltak köztük Suzuki szalonok új munkatársai és családok autófanatikus gyerekekkel. (14 év alattiak szülői kísérettel sem mehetnek be a prés- és a hegesztőüzembe, ők csak az összeszerelőüzemet nézhetik meg.)
A belföldi értékesítés vezetőjétől, a gyáralapítás óta a Suzukinál dolgozó Lelovics Sándortól megtudtuk, hogy a japánok azért döntöttek Esztergom mellett, mert az ottani táj hasonlít Japánra: hegyes-dombos, van víz (a Duna) a közelben és tiszta a levegő (bár elmondása szerint a volt orosz katonai lőtér miatt 1 évig kellett a terepet rendezni…). Visszaemlékezett arra is, hogy anno napi 1 autót gyártottak és 670000 Ft volt az eladási ára. (Ezzel szemben ma több mint 800 autót gyártanak naponta és pl. egy alapfelszereltségű Vitara listaára megközelíti az 5 millió Ft-ot.) Szó esett arról is, hogy az esztergomi gyár picinek számít. Nincs raktáruk és minden alkatrész Just-in-Time érkezik, tehát pont akkor, amikor szükség van rá. Ha a beszállító késik, csillagászati kötbért kell fizetnie a Suzukinak.
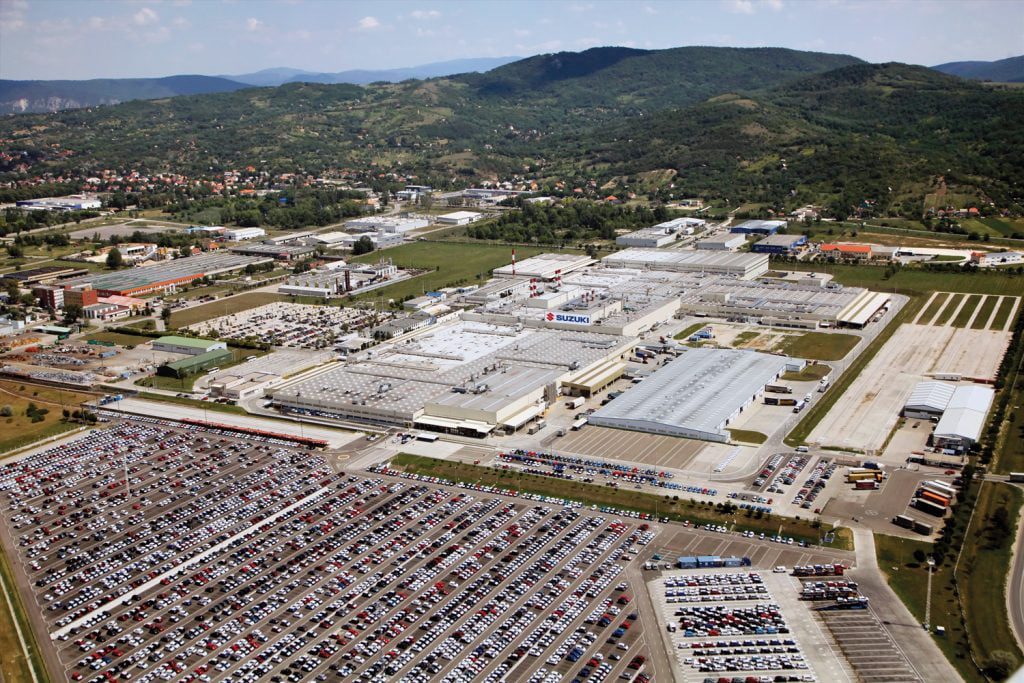
Egy másik szervező ismertette velünk a Suzuki történetét. Az 1909-ben alapított cég eredetileg szövőszékeket gyártott egy japán faluban, Hamamatsuban. Az 1930-as évek végén a vállalat már kisautók gyártására készült, de a második világháború miatt kénytelen volt leállítani a projektet. A háború után, 1952-ben került sor az első motorkerékpár és 1955-ben az első kisautó („a japán Trabant”) előállítására. Azóta is a kisautók gyártása a Suzuki fő profilja. Európában csak Esztergomban van gyáruk. Ezt a gyárat 1991-ben alapították és 1992. október 23-án gördült le az első Swift a gyártósorról. A 2008-as évben már 283000 autót gyártottak. A 2008-2009-es gazdasági válság következtében az eladások és a gyártás is rendkívüli mértékben visszaesett. Jelenleg kb. 170-180000 autót gyártanak évente. Ez annak is köszönhető, hogy pár évvel ezelőtt a Swift gyártása átkerült Indiába. Ez a lépés éves szinten 50000 autóval csökkentette az esztergomi gyár termelését. Jelenleg csak Vitarát és SX4 S-CROSS-t gyártanak. Egy autót 3,5 nap alatt állítanak elő.
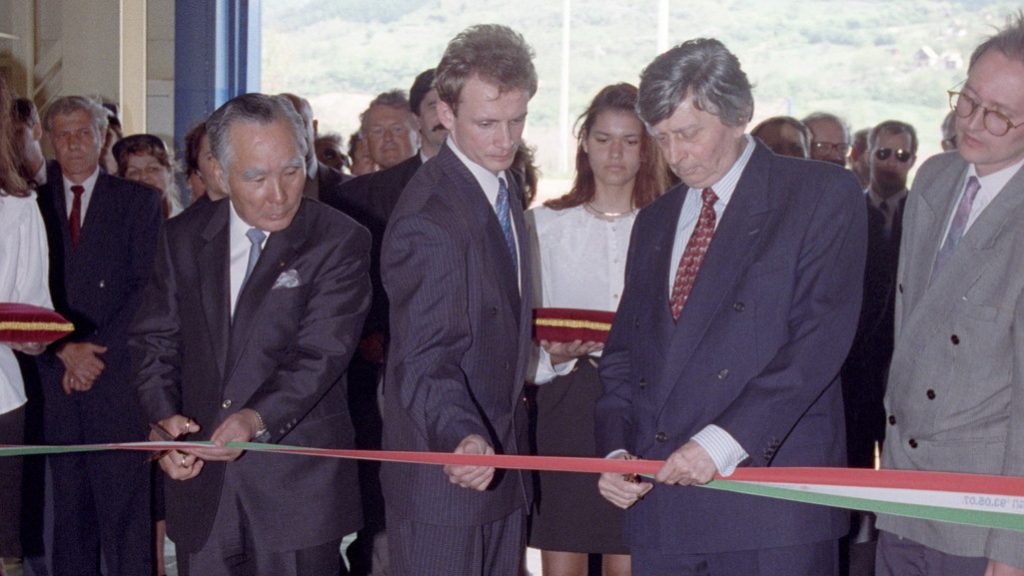
A bevezetők után levetített rövid filmből jobban megértettem a gyár felépítését és az egyes munkafázisokat. A présüzemben sík lemezekből készítik a különféle paneleket Japánból hozott szerszámgépekkel. A hegesztőüzemben az alkatrészek, elemek ponthegesztése és a karosszéria összeállítása történik. A festőüzemben egy alapos tisztítást követően történik a felületaktiválás, majd a festés, a lakkozás és a rozsdagátlás. Ezután 45 percet töltenek az elemek egy kemencében és miután megszáradtak, egy alapos minőség ellenőrzést követően átkerülnek a szerelőüzembe. Ugyanoda futnak be a lökhárító üzemből a fröccsöntött műanyag alkatrészek, a műszerfal és az ajtóburkolatok.
A film után csoportokra osztottak minket – tipikusan 10-12 fős csoportok szoktak lenni, de mi csak hatan voltunk -, majd kaptunk egy-egy headset-et, hogy a gyár zaja ellenére is halljuk, amit a csoportvezetőnk mond és elindultunk a présüzembe. Az üzem területén mindenhol felfestett útvonalakon, többnyire libasorban jártunk, a sarkokon „stop” és „nézz körül” feliratokat olvastunk a padlón és motivációs szövegeket a falakon. A legtöbb szöveg idézet volt magától Osamu Suzuki úrtól, aki arra biztatja a dolgozókat, hogy „mi legyünk a legjobbak”, „megoldjuk a válságot” és „csökkentsük a saját költségeinket”. A költségcsökkentési irányelvvel összhangban a gépek úgy vannak beállítva, hogy a lehető legkevesebb selejt termelődjön a lemezek vágása során. A présgépek előtt állva csoportunk vezetője hosszasan magyarázta a transzfer- és a tandemprések közti különbséget. Saját szemünkkel is meggyőződhettünk, hogy a transzferprés egy hatalmas gépsor, amelyen belül az egyes prések többféleképpen tudják megmunkálni az adott alkatrészt. A tandemprésnél (ahol sorba állított présgépekről van szó) azt figyelhettük meg, ahogy a robotkarok elvégzik az alkatrészek átadását egyik munkafázisból a másikba.
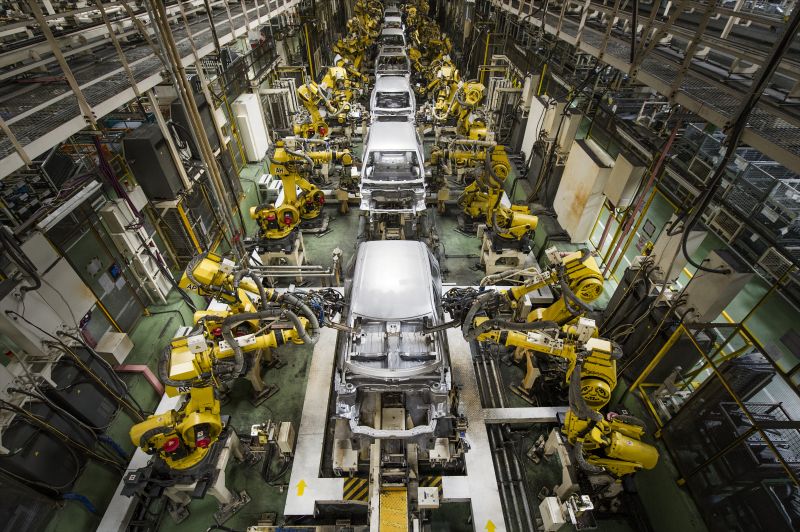
Míg a présüzemben munkásokat is láttunk, akik pl. a formára vágott ajtókat és motorháztetőket kivették a gépből, a hegesztőüzemben főként robotok dolgoztak. Itt az emberek legfeljebb a számítógépek beállítását végzik. Megtudtuk, hogy egy karosszéria 350 alkatrészből áll és összesen 4500 ponthegesztésre van szükség autónként. A ponthegesztés előnye, hogy nem ég vagy füstöl közben az anyag, a robotoké pedig az, hogy sokkal pontosabban tudnak dolgozni, mint az emberek és olyan helyeken is hozzáférnek az alkatrészekhez, ahova kézi hegesztés során nem lehetett. Kipróbálhattunk egy régi kézi hegesztőt, ami fel van függesztve és a súlyával balanszíroztatva, de még így is elképesztően nehéz. Nagyon jó kondiban kellett lennie annak, aki ezt a hegesztőgépet napi 8 órában használta. Tovább haladva megfigyelhettük azt is, hogy a karosszéria összeállításakor a robotok szenzorokkal érzékelik, hogy melyik fajta autón dolgoznak éppen és milyen alkatrészt kell kiválasztaniuk.
A szerelőüzemben láthattuk, hogy oda már a festett karosszéria érkezik meg a szállítószalagon. Ekkor az ajtókat leszedik, mert azok nélkül könnyebb hozzáférni az autó belsejéhez és azért is, mert az ajtókat még szintén meg kell szerelni. Ez könnyű fizikai munka és többnyire nők végzik. Az ajtók nélküli autók haladnak tovább egy szállítószalagon és közben, az egyes munkaállomásoknál dolgozók csapatai menet közben végeznek el munkafázisokat rajta. Aki nem az autóban ülve szerel valamit, az a szalagon sétálva, mozgás közben végzi a feladatát. A hibák jelzésére és a sor megállítására fejmagasságban elhelyezett sárga és piros szalagok szolgálnak. A dolgozókat bátorítják arra, hogy jelezzék, ha gond van, ne csináljanak és ne is engedjenek tovább hibát a folyamat során.
Figyeltük ahogy a helyére kerül az autókban a kárpit, az ülések, a kerekek, a szélvédő. A motort egy robot készíti a dolgozók keze alá és ketten emelik be a helyére. A szerelési folyamat vége felé kerül sor a műszerfal és az üzemanyagcső beépítésére. Az autókba töltenek annyi üzemanyagot, amennyi az első benzinkútig elég, majd behelyezik az akkumulátort is.
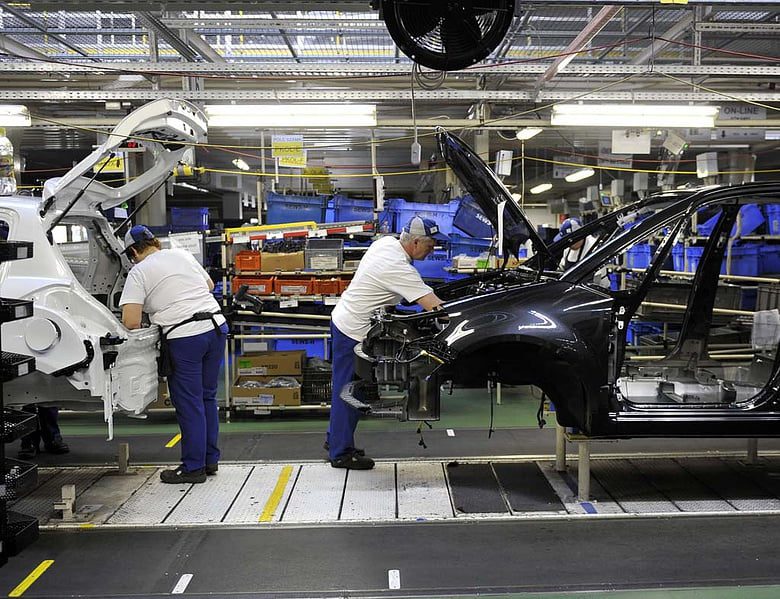
Egy munkafázisnak 71 másodperc alatt kell elkészülnie a Vitara és az SX 4 esetében is. (A Swift gyártásakor 63 másodperc volt az egy munkafázisra jutó idő.) Ez azt is jelenti, hogy 71 másodpercenként gördül le egy új Suzuki a szalagról! Az a fiatal nő, aki az egyik utolsó összeszerelési fázisként beül az autóba, helyére pattintja a kesztyűtartót, beindítja a motort és átgurul a másik sorra - hogy teszteljék, hogy működik-e az autó - egy 8 órás műszak alatt több mint 400-szor teszi ezt meg.
Egy ember egy munkafázist végez. Ha a csoportján belül ellesi a többi munkafázist, akkor egy idő után cserélgethet, hogy ne legyen annyira unalmas számára a munka. Opcionális dolog erre vállalkozni, de a fizetésemeléskor figyelembe veszik, hogy ki mennyire kész több feladatot is megtanulni. Egyébként a legelső lépés a frissen felvettek gyakorlatoztatása. Láthattuk a munkapadot, ahol 45 másodperc áll rendelkezésére a tanoncnak arra, hogy 15 csavart behúzzon. Állítólag 10 emberből legfeljebb 5 képes rá… De a vezetőnk elmondása szerint ilyenkor nem “selejtként” tekintenek azokra, akik nem teljesítették megfelelően ezt a feladatot, hanem kipróbálják őket más területeken. A cél az, hogy olyan feladatuk legyen, ami jól megy nekik és világbajnokok lehetnek benne.
Miután az autó megtette az első pár méterét, már csak a küszöb kerül a helyére és jöhet a végellenőrzés, amit mérnökök és technikusok végeznek. Ez magában foglalja többek közt a külső és belső terek ellenőrzését, a kerékösszetartás és a fényszórók beállítását, a futáspróbát és a fékek tesztelését. Azt már nem láttuk, ahogy az autók megkapták a szállítás elleni védelmüket (elsősorban fóliázást) és átkerültek a késztermék-parkolóba, ahonnan szállítmányozási cégek vasúton vagy teherautóval juttatják el őket a rendeltetési helyükre.
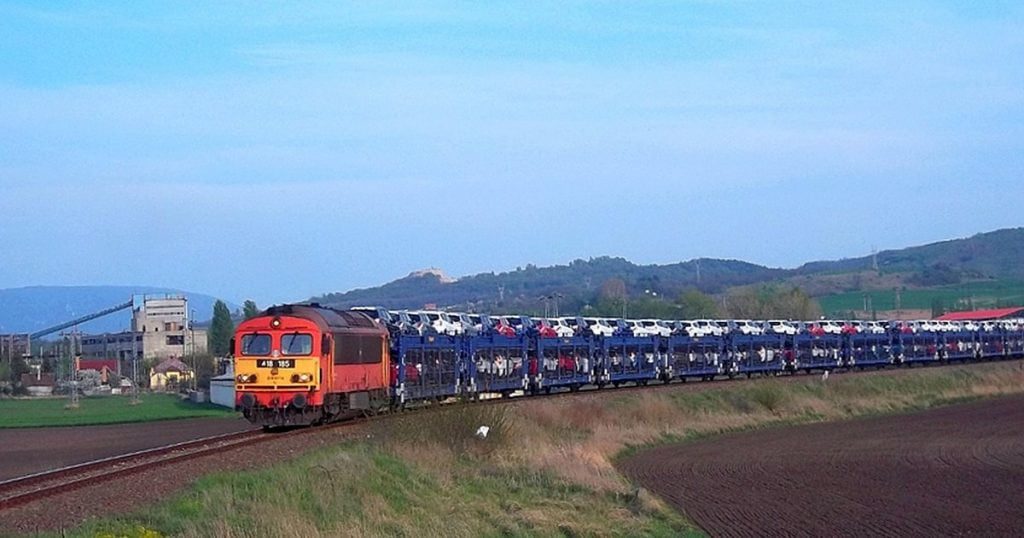
Ha kedvet kaptatok a Suzuki-gyár meglátogatásához, itt tudtok jelentkezni. Épp most hirdettek új időpontokat!
A fotók forrásai:
https://hipa.hu; https://www.autonavigator.hu; http://budapesttimes-archiv.bzt.hu;; https://www.hirado.hu
http://jarmuipar.hu; https://www.napi.hu; https://kesztolc.hu